Acteur majeur de l’industrie dentaire, Septodont fait face à une forte croissance de son marché. Après avoir construit une nouvelle unité de production de cartouches d’anesthésiques injectables sur son site de Saint-Maur à partir de 2016, le laboratoire pharmaceutique français travaille désormais à la mise en place d’un nouveau centre de distribution en Seine-et-Marne. Jean-Yves Doré partage avec nous les bonnes pratiques et les projets en cours de sa direction supply chain.
Pour poursuivre la lecture de ce contenu, abonnez-vous dès maintenant
Déjà abonné ? Identifiez-vous
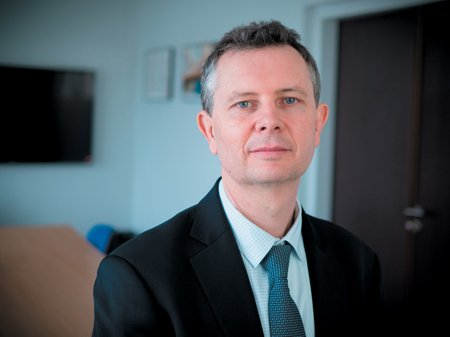
« Nous allons ouvrir un nouveau centre de distribution cet été »
Crédit photo Jean-Luc Rognon